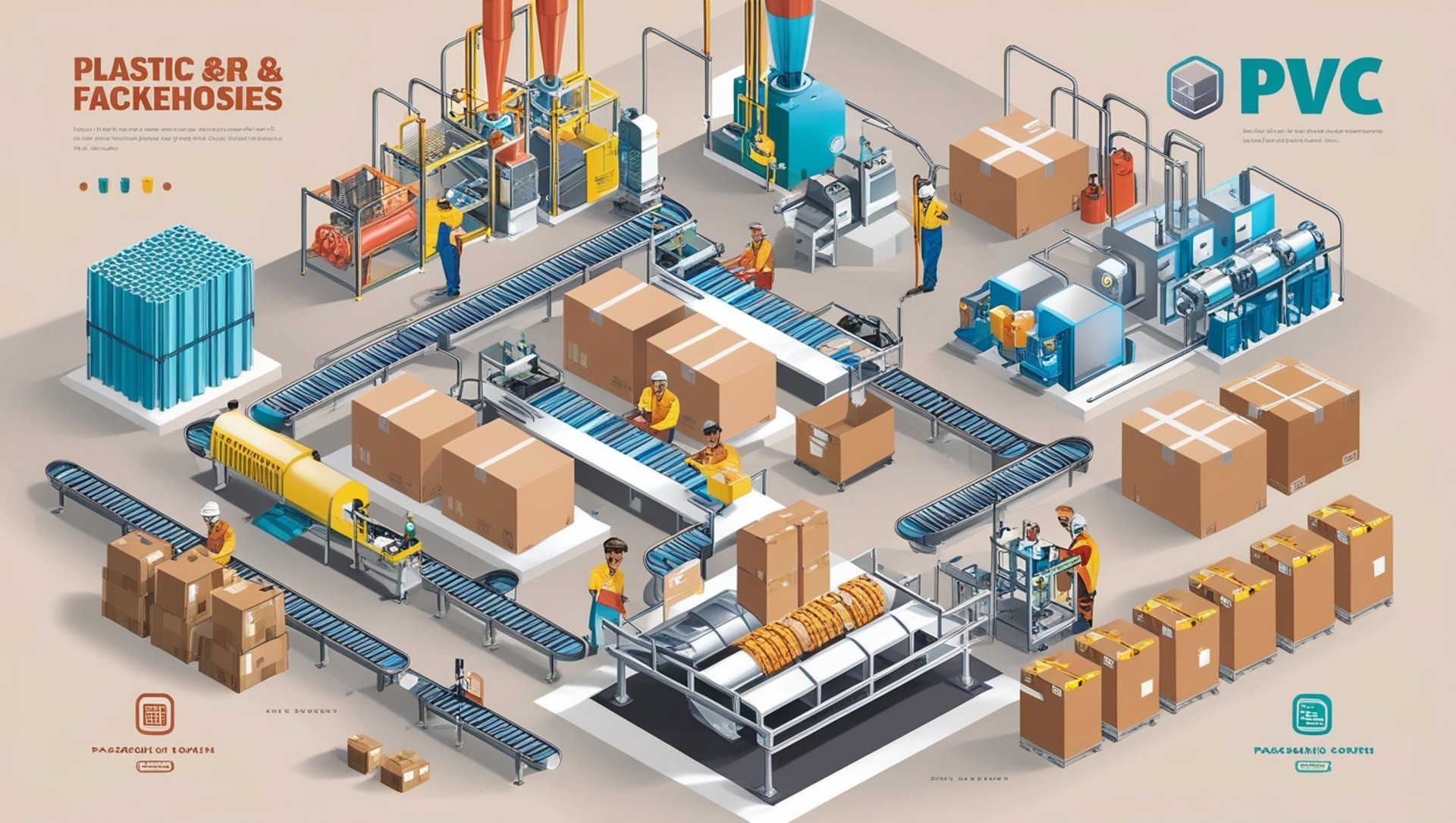
Master Plastic Pack Limited, a leading manufacturer of flexible packaging, wrapper printing, D-Boxes, and sheets, faced operational inefficiencies, high production costs, and supply chain challenges due to outdated systems. To streamline its operations, ensure real-time inventory tracking, and improve production planning, the company implemented Fibersoft ERP.
This case study explores the 10 major challenges Master Plastic Pack Limited faced and how Fibersoft ERP provided effective solutions to enhance efficiency, cost control, and business growth.
Challenges & Solutions
1. Inefficient Raw Material Management
Challenge:
Difficulty in tracking polymer, inks, solvents, adhesives, and films.
Over-purchasing or stock shortages led to production halts.
✅ Solution:
Automated material tracking ensures optimal stock levels.
Real-time consumption monitoring prevents shortages.
Supplier integration allows automated reordering.
2. Complex Production Scheduling
Challenge:
Multi-stage printing and packaging require precise scheduling.
Unplanned machine downtime delayed deliveries.
✅ Solution:
AI-powered production planning adjusts real-time schedules.
Machine maintenance alerts prevent unexpected breakdowns.
Workload balancing improves efficiency.
3. High Waste & Scrap Generation
Challenge:
Excessive material waste during printing, laminating, and slitting.
No system to track or optimize waste reduction.
✅ Solution:
Waste tracking module identifies high-waste areas.
Process optimization tools reduce scrap.
Reusability tracking enhances resource utilization.
4. Quality Control & Compliance Risks
Challenge:
Maintaining print accuracy, adhesion strength, and durability was difficult.
Compliance with ISO, FDA (food-grade packaging), and local regulations required extensive paperwork.
✅ Solution:
Automated quality checks ensure consistency in packaging.
Regulatory compliance tracking minimizes errors.
Barcode & RFID tracking ensure batch traceability.
5. Inefficient Order Processing & Customization Handling
Challenge:
Custom orders (sizes, designs, coatings) caused order processing delays.
Manual coordination between design, production, and delivery led to errors.
✅ Solution:
CRM-integrated order processing eliminates miscommunication.
Automated design approvals streamline custom orders.
Real-time tracking ensures timely delivery.
6. Delayed Deliveries & Logistics Challenges
Challenge:
Poor fleet coordination caused delays in packaging shipments.
High transportation costs due to inefficient route planning.
✅ Solution:
Logistics and route optimization tools reduce costs.
Multi-warehouse visibility ensures fast dispatch.
Integrated order tracking improves customer communication.
7. Weak Financial & Cost Control
Challenge:
Pricing inaccuracies affected profitability.
Manual financial tracking caused tax compliance issues.
✅ Solution:
Automated cost tracking & pricing models optimize profitability.
Tax compliance automation reduces errors in GST, VAT, and customs.
Multi-currency handling simplifies exports.
8. Lack of Real-Time Data for Decision-Making
Challenge:
No centralized data system for inventory, production, and sales.
Managers lacked real-time insights for quick decision-making.
✅ Solution:
Cloud-based dashboard provides real-time data.
AI-driven analytics predict demand and optimize production.
Customizable reports improve strategic planning.
9. Vendor Management Issues
Challenge:
Dependence on external vendors for specialized printing.
Lack of tracking for outsourced processes.
✅ Solution:
Vendor management system ensures reliable subcontracting.
Automated purchase orders improve supplier coordination.
Performance tracking helps optimize vendor selection.
10. Workforce Productivity & HR Management
Challenge:
Manual payroll & attendance tracking led to inefficiencies.
Lack of workforce analytics impacted labor efficiency.
✅ Solution:
HRM module with biometric integration ensures accurate attendance tracking.
Payroll automation reduces errors.
Employee productivity monitoring optimizes workforce allocation.
Results After Implementing Fibersoft ERP
Master Plastic Pack Limited saw significant improvements across all departments:
📉 30% reduction in material waste through efficient tracking.
📦 25% faster order fulfillment due to optimized scheduling.
💰 20% cost savings in raw material procurement.
🚚 35% improvement in on-time deliveries with logistics integration.
📊 Enhanced decision-making with real-time analytics.
Conclusion
By implementing Fibersoft ERP, Master Plastic Pack Limited successfully transformed its operations, achieving better inventory control, efficient production planning, waste reduction, and financial accuracy. The ERP’s automation, AI-driven analytics, and cloud accessibility positioned the company for sustainable growth in the competitive packaging industry.😊
Fibersoft ERP
Mobile .: 0300 3360042
Email: info@fibersoft.online

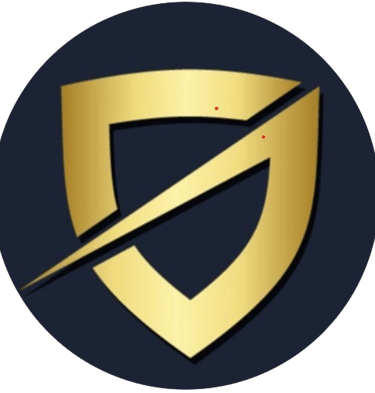
Contact Us
Phone .: 055 4257900
City Office: 501/6, PSO Baghbanpura, GRW-PAK
Quick Links
Head Office: A-81 University Town, GRW-PAK